Installing and maintaining single check valves in large-scale industrial systems can pose several challenges. Some of these challenges include:
1.Proper Sizing: In large-scale industrial systems, accurately sizing single check valves is essential to handle the substantial flow rates and varying pressures. Hydraulic analysis and detailed calculations are necessary to select valves that can meet the demands of the system without causing excessive pressure drops or inefficiencies.
2.Installation Location: Identifying the optimum installation points for single check valves is a critical consideration. Factors such as proximity to potential backflow sources, ease of access for maintenance, and compatibility with existing piping configurations must be carefully evaluated to ensure effective prevention of backflow while facilitating routine inspections.
3.Pipeline Layout: Designing the pipeline layout is complex in large industrial systems. Engineers must account for the placement of single check valves in a manner that minimizes turbulence, pressure losses, and uneven fluid distribution. Computational fluid dynamics (CFD) simulations are often employed to optimize the pipeline design.
4.Material Compatibility: Selecting materials for single check valves is vital to prevent corrosion and maintain structural integrity. Industrial fluids can vary widely in composition and aggressiveness. Conducting material compatibility tests and consulting corrosion engineers ensures that the chosen materials can withstand the specific chemical properties of the fluids being processed.
5.Maintenance Access: Accessibility is a major concern in large industrial facilities where pipelines are often densely packed. Planning maintenance access points strategically, incorporating features like removable insulation and access panels, can facilitate efficient inspection and repair procedures without disrupting the entire system.
6.Pressure Fluctuations: Managing pressure fluctuations is challenging, particularly in systems with variable demands or dynamic processes. Pressure relief valves, surge suppressors, or accumulator tanks might be necessary to mitigate sudden pressure spikes, protecting single check valves from premature wear due to water hammer or other hydraulic shocks.
7.Temperature Extremes: Large industrial systems often operate under extreme temperature conditions. Single check valves must be selected or customized to withstand these temperature fluctuations without compromising their mechanical properties. Thermal expansion and contraction considerations are crucial to prevent leakage or valve failure.
8.Fluid Contamination: Industrial fluids may contain particulates or impurities that can obstruct valve internals, leading to reduced efficiency or complete valve failure. Employing effective filtration systems and implementing regular fluid analysis protocols can help mitigate the risk of contamination, ensuring the longevity of single check valves.
9.Maintenance Expertise: Skilled technicians are essential for the installation, maintenance, and repair of single check valves. Providing training programs and investing in continuous education for maintenance personnel ensures that they are proficient in the latest technologies and best practices, enhancing the overall reliability of the system.
10.Seal Integrity: Proper sealing mechanisms are critical in preventing leaks. Regular inspection and replacement of seals and gaskets, especially in high-pressure applications, are essential maintenance tasks. Employing advanced sealing materials and designs can enhance the longevity and reliability of single check valves.
11.Regulatory Compliance: Compliance with industry standards and regulations is paramount. Engaging with regulatory bodies, staying updated with evolving standards, and conducting regular audits to ensure adherence to compliance requirements are necessary steps in maintaining the legal and operational integrity of the industrial system.
12.Cost Management: Managing costs while maintaining quality is a constant challenge. Conducting a total cost of ownership analysis, considering factors such as initial procurement, maintenance, energy efficiency, and downtime costs, helps in making informed decisions about the selection and maintenance of single check valves. Collaboration with reliable suppliers and adopting proactive maintenance strategies can also contribute to cost optimization.
SINGLE CHECK VALVE
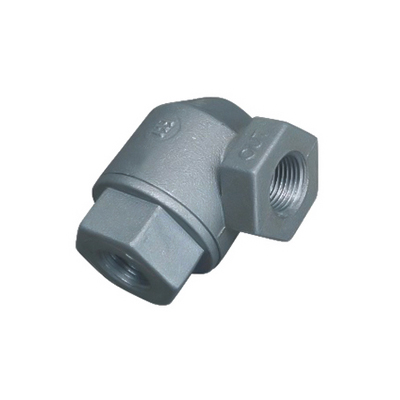
SINGLE CHECK VALVE
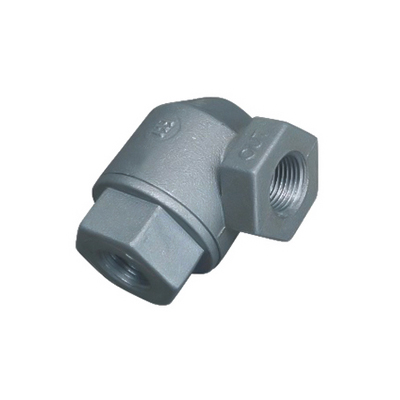