The reliability of a foot brake valve in terms of consistent braking performance largely depends on several factors:
Quality of Manufacturing: The reliability of a foot brake valve hinges on the intricacies of its manufacturing process. Advanced machining technologies, such as CNC (Computer Numerical Control) machining, enable precise fabrication of intricate components to tight tolerances. Quality manufacturers employ rigorous inspection protocols throughout production, utilizing techniques like coordinate measuring machines (CMM) and optical inspection systems to verify dimensions and detect any defects. Additionally, automated assembly processes ensure consistent assembly quality, reducing the likelihood of assembly errors that could compromise reliability.
Material Quality: The choice of materials profoundly influences the performance and durability of a foot brake valve. For instance, the valve body and critical components may be machined from high-strength alloys or engineered plastics to withstand the stresses of braking forces and environmental conditions. Sealing materials undergo extensive testing to ensure they maintain their integrity under high pressures and temperatures, resisting degradation from brake fluids and contaminants. Furthermore, surface treatments such as anodizing or plating enhance corrosion resistance and wear characteristics, prolonging the valve's service life.
Maintenance: Comprehensive maintenance practices are essential for preserving the reliability of a foot brake valve throughout its operational lifespan. Maintenance schedules, outlined by the manufacturer, delineate specific intervals for inspection, servicing, and replacement of components. Skilled technicians conduct thorough inspections, utilizing diagnostic tools like pressure gauges and leak detectors to assess the valve's condition. Cleaning procedures involve the use of specialized solvents and equipment to remove contaminants without damaging sensitive components. Lubrication protocols specify the type and quantity of lubricants required to ensure smooth operation of moving parts while preventing excess buildup that could attract debris.
Environmental Factors: The operational environment poses significant challenges to the reliability of foot brake valves. Harsh conditions, such as extreme temperatures, humidity, and exposure to corrosive substances, can accelerate wear and deterioration of materials. To mitigate these risks, manufacturers employ robust design strategies, such as selecting materials with superior resistance to environmental factors and incorporating protective features like seals and gaskets. Environmental testing, including exposure to temperature extremes, salt spray, and chemical agents, validates the valve's performance under adverse conditions, ensuring reliability in real-world scenarios.
Compatibility with the Vehicle: Achieving seamless integration with the vehicle's braking system is paramount for ensuring the reliability of a foot brake valve. Engineering teams collaborate closely with vehicle manufacturers to tailor the valve's design and specifications to the unique requirements of each application. Compatibility considerations encompass factors such as hydraulic or pneumatic system architecture, mounting configurations, and interface compatibility with other components. Rigorous testing protocols, including bench testing and vehicle validation tests, validate the valve's performance within the intended application, ensuring optimal reliability and safety.
USA TURCK FOOT BRAKE VALVE
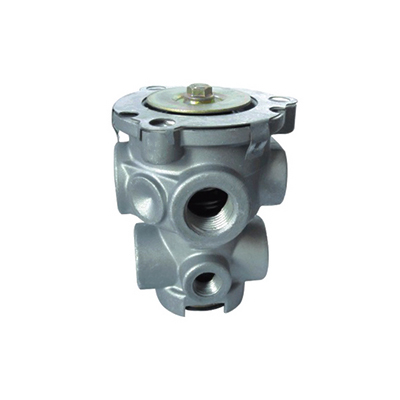
USA TURCK FOOT BRAKE VALVE
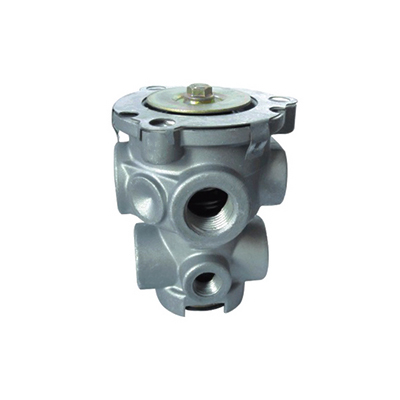