Quick Release Valve (QRV) is a type of valve used in pneumatic and hydraulic systems to rapidly release pressure in a controlled manner. Its primary function is to facilitate the quick and efficient exhaust of compressed air or hydraulic fluid from a system, allowing for rapid decompression.
Here's a basic explanation of how a Quick Release Valve operates and its primary functions:
Operation:
1.Normally Closed Position: The Quick Release Valve is meticulously designed to maintain a normally closed position during standard operational phases, effectively sealing off the passage for fluids or gases. This configuration ensures system stability, preventing any inadvertent release of pressure that could compromise operational safety. The sealing mechanism, which may involve high-quality seals or precision machining, is critical for the reliability of the closed state, especially in applications where tight control over pressure is essential.
2.Activation: Activation mechanisms exhibit a spectrum of sophistication, ranging from manual controls to intricate automated systems. Manual control options could involve ergonomic levers designed for quick and decisive action, while automated systems might incorporate advanced sensors and electronic controls for precise, high-speed responses. Considerations for the design of the actuation system involve factors such as response time, reliability, and the incorporation of fail-safe features to ensure the Quick Release Valve performs optimally in emergency situations.
Primary Functions:
1.Emergency Pressure Release: In emergency scenarios, the Quick Release Valve becomes a frontline defense mechanism, rapidly responding to triggers or signals indicating a critical situation. The controlled release of pressure is not only a safety imperative but also involves intricate engineering to manage the sudden surge of fluid or gas without causing system shocks or damage. Fail-safe mechanisms, redundancy, and rigorous testing are vital components of a reliable Quick Release Valve, ensuring its effectiveness when it matters most.
2.Braking Systems: Within hydraulic braking systems, the Quick Release Valve plays a pivotal role in the delicate balance between rapid response and controlled release. Hydraulic systems demand precision, and the valve's contribution to quick brake disengagement involves considerations of fluid dynamics, response time, and integration with other braking components. Ongoing research and development in this area aim to enhance braking efficiency, reduce stopping distances, and improve the overall safety of vehicular transportation.
3.Pneumatic Systems: The application of Quick Release Valves in pneumatic systems extends to diverse industrial sectors where compressed air is a primary power source. Achieving rapid decompression involves considerations of airflow dynamics, valve size, and compatibility with the broader pneumatic infrastructure. Users benefit not only from the immediate pressure relief but also from the efficiency gains and precision control offered by well-designed Quick Release Valves.
4.Energy Efficiency: Quick Release Valves contribute significantly to the energy efficiency of systems by promptly releasing stored energy when it is not required. This energy-conscious approach involves intricate design considerations, such as optimizing valve geometry, minimizing internal friction, and utilizing materials that facilitate rapid response times.
5.Reducing System Stress: The controlled release of pressure at strategic points in the system is a linchpin in minimizing stress on critical components. Engineers meticulously analyze stress points, material fatigue, and the effects of pressure differentials to design Quick Release Valves that not only perform reliably but also contribute to the overall robustness of the system. Finite element analysis, stress testing, and ongoing monitoring are integral to the development and maintenance of systems where Quick Release Valves are deployed.
QUICK RELEASE VALVE
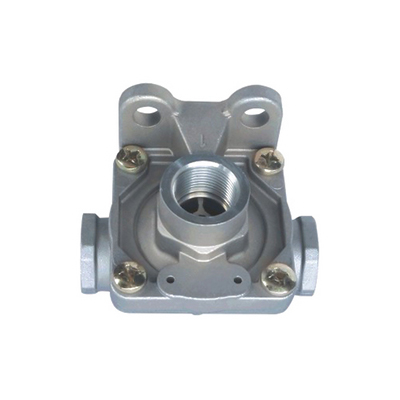
QUICK RELEASE VALVE
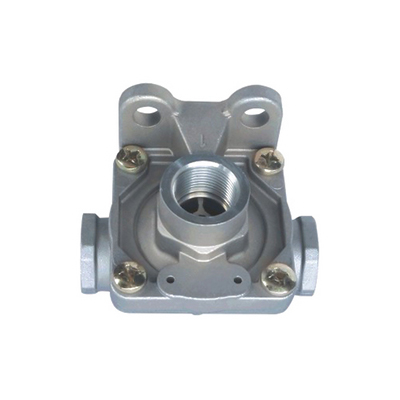