Different types of brake chambers can significantly impact braking performance and reliability due to variations in design, construction, and functionality. Here's how:
Size and Volume: The size of a brake chamber is crucial in determining its air compression capacity and subsequent braking force output. Larger chambers have greater internal volume, allowing them to compress more air, which translates to higher braking force. This makes them indispensable for heavy-duty vehicles that require substantial stopping power. Conversely, smaller chambers, while offering quicker response times due to their lower volume, may lack the force necessary for larger vehicles. It's essential to select the appropriate chamber size based on the vehicle's weight, load, and intended application to ensure optimal braking performance and safety.
Type of Brake: Service brake chambers and spring brake chambers serve distinct yet complementary functions within a vehicle's braking system. Service brake chambers are primarily responsible for regular braking operations, activated when the driver applies the brake pedal. These chambers convert air pressure into mechanical force to engage the brake shoes or pads against the drum or rotor, facilitating vehicle deceleration. In contrast, spring brake chambers act as an emergency brake system, automatically engaging the brakes when air pressure is lost, typically due to system failure or air leakage. This dual-chamber system provides redundancy and enhances vehicle safety by ensuring braking capability even in adverse conditions.
Construction Materials: Brake chambers are constructed from various materials, each offering unique advantages in terms of durability, weight, and resistance to environmental factors. Steel chambers are renowned for their exceptional strength and durability, making them suitable for heavy-duty applications. However, their weight can impact vehicle efficiency and fuel consumption. Aluminum chambers provide a lightweight alternative without compromising durability, ideal for applications where weight reduction is critical. Additionally, composite materials, such as reinforced plastics, offer a balance of strength and weight savings, along with resistance to corrosion and chemical damage, making them well-suited for harsh operating environments.
Sealing Mechanisms: The sealing mechanism of a brake chamber plays a pivotal role in maintaining air pressure integrity and ensuring reliable braking performance. High-quality seals, typically composed of resilient materials such as rubber or synthetic elastomers, create a tight barrier to prevent air leakage. Proper sealing is essential to sustain optimal brake chamber functionality, as even minor leaks can lead to reduced braking effectiveness, increased stopping distances, and potential safety hazards. Advanced sealing technologies, including lip seals, O-rings, and piston seals, enhance durability and longevity, minimizing maintenance requirements and downtime.
Internal Components: Within a brake chamber, several internal components work in concert to convert air pressure into mechanical force and regulate braking action. The primary component is the diaphragm, a flexible membrane that expands and contracts in response to changes in air pressure. This movement actuates the pushrod, which in turn applies force to the brake mechanism. Springs assist in brake release and provide return force to retract the pushrod when air pressure is released. Valves control the flow of air within the chamber, governing brake application and release for precise control. Optimal design and engineering of these internal components ensure smooth operation, consistent braking performance, and resistance to wear and fatigue under demanding operating conditions.
SPRING BRAKE CHAMBER
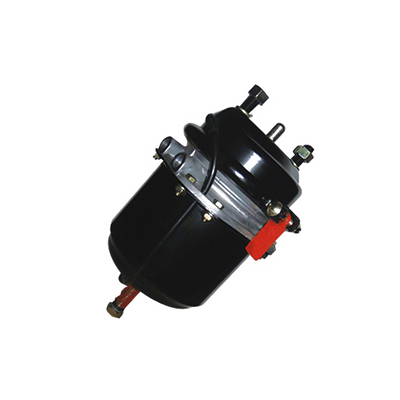
SPRING BRAKE CHAMBER
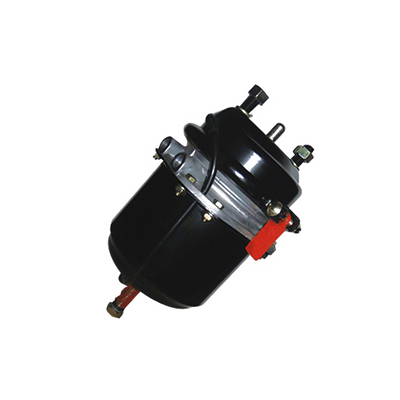